Episodes
![Ep 34 Node-Red for IIoT in the Enterprise - [ Nick O’Leary, CTO Flowforge Inc ]](https://pbcdn1.podbean.com/imglogo/image-logo/9018806/podcast_cover1400x1400_2xi99v_300x300.png)
Tuesday Apr 11, 2023
Ep 34 Node-Red for IIoT in the Enterprise - [ Nick O’Leary, CTO Flowforge Inc ]
Tuesday Apr 11, 2023
Tuesday Apr 11, 2023
The Node-Red project turns ten this year.🎉
And yet, its remarkable potential remains largely untapped in the industrial software domain.
Having been a Node-Red user and promoter since its early days, I've observed that its preparedness for enterprise deployments is a key challenge limiting its broader adoption.
To discover the most effective strategies for deploying and managing enterprise-grade Node-Red applications in Industrial IoT, I invited Nick O'Leary for a podcast conversation.
As the co-creator of Node-Red and the CTO and Founder of FlowForge—a DevOps platform for Node-Red—Nick brought invaluable insights to the discussion.
Below is the outline of our discussion.
✅ Origins and Evolution of Node-Red
✅ Challenges and best practices for deploying Node-RED in Industrial environments
✅ DevOps for Node-RED in IIoT
✅ Key Features of Enterprise Ready Node-RED
✅ Best practices for industrial data acquisition using Node-Red
✅ Suitability of Node-Red for Semantic Modelling
✅ Node-Red vs Off-Shelf Solutions
✅ Use cases for Edge vs Cloud deployment of Node-Red
✅ Best Practices for Scaling Node-Red in large-scale IIoT deployments.
✅ Access control, data encryption, and authentication in Node-Red.
✅ Examples of successful IIoT projects using Node-Red
✅ The Future of Node-Red in Industrial IoT Applications
![Ep 33 Unified Namespace for Industrial IoT: The Masterclass - [ Walker D Reynolds, 4.0 Solutions ]](https://pbcdn1.podbean.com/imglogo/image-logo/9018806/podcast_cover1400x1400_2xi99v_300x300.png)
Monday Apr 03, 2023
Monday Apr 03, 2023
Digital transformation of a manufacturing enterprise is a complex process that goes far beyond simply sending data to the cloud and implementing “predictive maintenance”.
It requires a strategic architectural approach that effectively utilizes your data ecosystem to make informed decisions in real-time and drive innovation at every level of your organization.
While there are various architectural approaches, the Unified Namespace (UNS) stands out as the most effective approach to achieve optimal results and reap the full economic benefits of digital transformation.
The UNS serves as a critical building block for your overall strategy.
I had the pleasure of interviewing Walker Reynolds, the President of 4.0 Solutions, a renowned industrial IoT expert who introduced and popularized UNS. He provides a masterclass on understanding, implementing, and benefitting from the Unified Namespace approach.
If you'd like to gain a solid understanding of leveraging the Unified Namespace for your manufacturing enterprise, don't miss out on this valuable conversation.
Outline
✅ Origins and evolution of Unified Namespace
✅ A Description of the Unified Namespace
✅ Why MQTT is the de-facto protocol for UNS implementation
✅ The role of MQTT Sparkplug in UNS Implementation
✅ The role of OPC UA in UNS Implementation
✅ Workflow for designing a Unified Namespace for IIoT System
✅ Mapping physical assets and devices to a Unified Namespace, tools and techniques.
✅ Metadata definition for consistency and accuracy across different systems and devices in UNS
✅ How MES fits into UNS architecture, specific functions and capabilities
✅ Challenges and Mitigation strategies in implementing a Unified Namespace
✅ Impact of Industry4.0 Community Discord Platform
✅ Industry4.0 Influencer Lists
✅ Impact of ChatGPT on Digital Transformation
#iot #iiot #industry40 #industrialiot #uns
![Ep 32 Low Foot Print OPC UA Over TSN for Real-Time Communication - [ Melvin Francis, Be Services ]](https://pbcdn1.podbean.com/imglogo/image-logo/9018806/podcast_cover1400x1400_2xi99v_300x300.png)
Thursday Mar 30, 2023
Thursday Mar 30, 2023
In this latest episode, I explore the capabilities of OPC UA PubSub and how it can be integrated with Time Sensitive Networking (TSN) to standardize industrial field-level data transfer.
I speak with Melvin Francis, the Project Manager for OPC UA and TSN-related services at BE.services GmbH, to discuss the challenges faced in developing related applications due to the lack of ready-made OPC UA + TSN stacks or SDKs.
We also delve into the value of OPC UA + TSN integration and how it can address the requirements of time-critical industrial systems.
Furthermore, we explore the ongoing research project by BE Services, in partnership with Hochschule Offsberg University, the German government, and various hardware vendors, to develop a hardware and OS-independent low-footprint OPC UA + TSN SDK for wired and wireless TSN networks.
Below is the outline of our conversation.
✅ How Time Sensitive Networking (TSN) Works
✅ OPC UA PubSub + TSN Integration
✅ Low-footprint OPC UA PubSub TSN Architecture
✅ SDK Test Suite for low-cost testing ecosystem
✅ Practical Demonstration
![Ep 31 Architecting IIoT Solutions Using Unified Namespace - [ David Schultz, G5 Consulting ]](https://pbcdn1.podbean.com/imglogo/image-logo/9018806/podcast_cover1400x1400_2xi99v_300x300.png)
Monday Dec 12, 2022
Monday Dec 12, 2022
The Unified Namespace has countless advantages over traditional architectural approaches when it comes to IIoT implementation in manufacturing.
Some of these are:
👉 More efficient communication and data sharing between different devices and systems.
👉 Improved scalability due to a unified interface that is consistent across the entire enterprise network.
But how do you go actually go about building a Unified Namespace Architecture?
To gain an understanding of this, I invited David Schultz for a podcast session.
David is the President of G5 Consulting where he works with manufacturers to help them develop and execute strategies for their digital transformation and asset management initiatives.
Below is the outline of our conversation.
✅ What is The Unified Namespace?
✅ MQTT/Sparkplug for Unified Namespace
✅ Tools and Strategies for Building the Unified Namespace
✅ Data Normalisation and Contextualisation Techniques for UNS
✅ Role and Significance of ISA 95 Schema in UNS
✅ Using Multiple MQTT Brokers for a Unified namespace
✅ Role played by Historian, MES, and ERP in UNS Architecture
✅ Use Cases and Technologies for Data lake Integration with UNS
✅ Approaches for Extending UNS with transactional Capabilities
![Ep 30 Fundamentals of OPC UA Information Modelling - [ Jouni Aro - CTO, Prosys OPC ]](https://pbcdn1.podbean.com/imglogo/image-logo/9018806/podcast_cover1400x1400_2xi99v_300x300.png)
Sunday Oct 23, 2022
Sunday Oct 23, 2022
When you look around a factory, you are likely to see objects interacting with other objects. And there are specific things that each object can do.
It, therefore, makes sense that, in order to build autonomously reconfiguring factories, each object needs to be able to describe its capabilities to other objects so that they can interact with no human intervention.
OPC UA Information Modelling is an effort to enable the description of complex industrial systems through a standardised and object-oriented interface.
To gain a deeper understanding of how it works, I invited Jouni Aro for a podcast conversation.
Jouni is the Chief Technology Officer at Prosys OPC Ltd, a leading provider of OPC and OPC UA technology with over 20 years of experience in the field. He's been the main architect for Prosys OPC UA SDKs and is an active member of the Technical Advisory Council and several working groups of the OPC Foundation.
Below is the outline of our conversation
✅ What is OPC UA Information Modelling
✅ Benefits of Information Modelling for Industry 4.0
✅ OPC UA Unified Object Model for Description of Complex Systems
✅ Tools for Building and Managing OPC UA information models
✅ OPC UA Companion Specifications, Custom Information Models
✅ OPC Cloud Library, Online Information Model Repository
✅ Workflow for integrating OPC UA Information Model into Products
✅ OPC UA Information Modelling in Industrial System Integration
✅ OPC UA Information Modelling and ISA95
✅ OPC UA Information Modelling for Vertical Integration
✅ OPC UA Information Modelling for Horizontal Integration
✅ Is OPC UA Information Modelling Future-Proof?
✅ Information Modelling for OPC UA PubSub Over MQTT
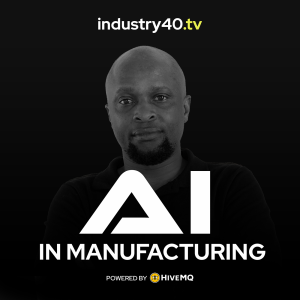
Thursday Oct 13, 2022
Thursday Oct 13, 2022
Gaining competitive advantage is the main driver of innovation in nature as much as it is in technology. And the manufacturing ecosystem is no different.
In manufacturing, this manifests in the deployment of production automation systems on the shop floor, and enterprise planning systems on the top floor.
But yet, there's a grey area in between that has, for the most part, remained underutilised or wrongly implemented altogether.
This is where a Manufacturing Execution System (MES) would live.
To understand how manufacturers can gain a competitive advantage by leveraging a Modern MES Architecture for data-driven manufacturing, I invited Kevin Jones for a podcast conversation.
Kevin is the CEO and Lead Strategist at Ectobox, Inc., a Manufacturing Intelligence Solutions company and
Industry 4.0 systems integrator based in Pittsburgh, PA.
Below is the outline of our conversation
✅ Drivers for Data-Driven Manufacturing
✅ Introducing MES for Manufacturing
✅ Functions of Manufacturing Execution Systems
✅ Selecting and Implementing an MES System
✅ Modern Manufacturing Execution System Architecture
✅ Problems with Current Manufacturing Data Systems
✅ Unified Namespace for Manufacturing Execution System
✅ Brownfield Integration into Unified Namespace Architecture
✅ The Future of MES in Manufacturing
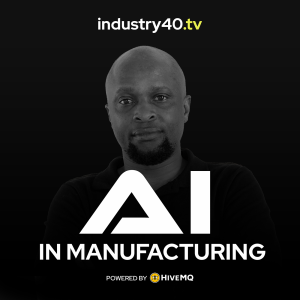
Thursday Oct 06, 2022
Ep 28 Predictive Analytics in Manufacturing - Maciek Wasiak, CEO Xpanse AI
Thursday Oct 06, 2022
Thursday Oct 06, 2022
I invited Maciek Wasiak for a podcast conversation on Predictive Analytics in Manufacturing and he delivered a masterclass.
Maciek is the CEO and Founder of Xpanse AI, a company that develops technology that rapidly accelerates Data Science delivery by replacing manual data science with AI-driven processing
Here's the outline of our conversation:
✅ Xpanse AI
✅ Introduction to Predictive Analytics
✅ Real-World Data Science Use Cases in Manufacturing
✅ Semiconductor Fabrication Predictive Analytics Solution Demo
✅ Traditional vs Automated Predictive Analytics
✅ Predictive Analytics Workflow Based on AI and ML
✅ Identifying and qualifying plant-floor data sources for Predictive Analytics
✅ Managing plant-floor data variety for Predictive Modelling
✅ Predictive Modelling Techniques
✅ Meeting plant-floor real-time requirements with ML Processes
✅ Role played by domain-level expertise in Predictive Analytics
✅ Role Played by Industrial System Integrators in Predictive Analytics implementation
✅ Working with AI and ML platforms for non data scientists
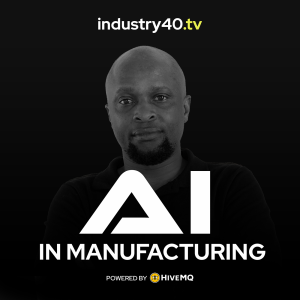
Thursday Sep 29, 2022
Thursday Sep 29, 2022
Whenever you're faced with information overload on any subject matter, as is the case with many manufacturers considering Smart Manufacturing, it's important to take a step back and understand its first principles.
Without which it would be difficult and costly to realise the vision of Smart Manufacturing.
To help bring the First Principles of Smart Manufacturing to light, I invited Conrad Leiva for a podcast conversation. Conrad is the VP of Ecosystem and Workforce Development at the Clean Energy Smart Manufacturing Innovation Institute, CESMII.
CESMII is a US Government funded institute with a mission to democratise Smart Manufacturing and make its methodologies and technologies more affordable and accessible to SME manufacturers.
Here's the outline of our conversation
✅ Clean Energy Smart Manufacturing Innovation Institute (CESMII)
✅ A Brief History of Smart Manufacturing
✅ Smart Manufacturing Definition and Description of Key Terms
✅ The Seven Principles of Smart Manufacturing
✅ Flat and Real-Time Principle
✅ Scalability Principle, Enabled by Cloud and Edge
✅ Interoperable and Open Principle, Information Modelling
✅ The Role of ISA 95 in Smart Manufacturing
✅ Proactive and Semi-Autonomous Principle
✅ Sustainable and Energy Efficient
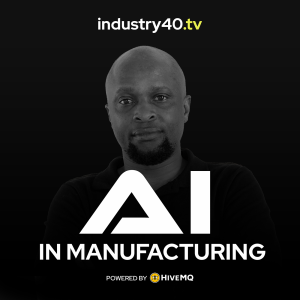
Thursday Sep 22, 2022
Thursday Sep 22, 2022
More than anything else, the foundational power of personnel in fieldwork merely lies in the fact that we can see.
By extension, it makes sense that the biggest impact on industrial digital transformation will come from embedding vision in intelligent connected components.
More so when embedded vision and AI software are widely deployed in mobile and battery-powered field equipment.
To learn more about building this capability into industrial products, I invited Taylor Cooper for a chat on the podcast.
Taylor is the CEO and Principal Engineer at MistyWest where he's recently led the company in developing an Embedded Vision System on Module (MistySOM), based on the Renesas RZ/V2L processor, that enables the embedding of vision-based AI capabilities in field equipment.
Below is the outline of our conversation.
✅ Misty West, Embedded Vision & IIoT
✅ Latest Trends in Industrial IoT, and Chip Shortage
✅ Google IoT Core Retirement, IoT Boom and Bust
✅ MQTT in IIoT and Computer Vision
✅ Delivering AI Capabilities for IIoT with Renesas RZ/V2L Based System on Module
✅ Potential Applications of Low Power System on Module in Connected Intelligence,
✅ Workflow for developing Embedded Vision for Connected Products
✅ AI versus Rules-Based Image Processing in Embedded vision
✅ Selecting Embedded Vision Middleware
✅ Selecting wireless connectivity for Embedded Vision Applications
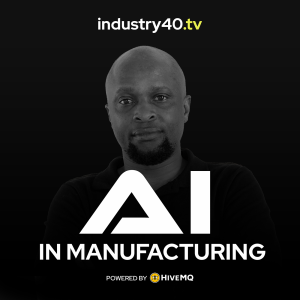
Thursday Sep 22, 2022
Thursday Sep 22, 2022
Here's the thing. Containerisation is not only an IT technology, it is an advanced IT technology. And yet, it already looms on the horizon for Operations Technology.
And, while the technology opens up massive opportunities for optimisation and efficiency in the OT network, it demands a fundamental rethink of industrial software distribution and management.
To find out what this actually means for vendors, engineers, and system integrators in the industrial space, I invited Neil Cresswell for a conversation.
Neil is the CEO and Co-Founder of a company called Portainer.io, the most popular Docker Container Management platform that abstracts the complexities of container management with a feature-rich and easy-to-use Graphical User Interface.
Below is the outline of our conversation.
✅ What are containers?
✅ Benefits of containerisation at the Industrial Edge
✅ Challenges of adopting containers for Industrial Edge Compute
✅ Key differences between containerisation at the edge and in the cloud
✅ Containerization Approaches and Microservices for IIoT
✅ What is Portainer and How it Works
✅ Use Cases in Industrial IoT
✅ Portainer Products
✅ Reference Architectures for Managing software in OT
✅ Best Practices Containerisation at the Industrial Edge
✅ How a Containerised PLC functions
✅ Impact of Containerisation on Industrial System Integration
✅ The Future of Industrial Software Distribution