Episodes
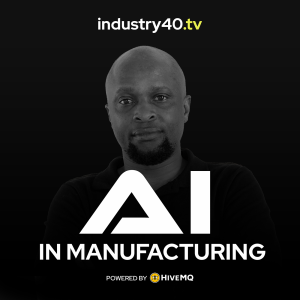
Wednesday Mar 19, 2025
Wednesday Mar 19, 2025
Manufacturing leaders are familiar with physical waste; scrap, rework, and inefficiencies in production.
But digital waste is the hidden inefficiency thatโs just as costly.ย It includes:
๐๐ง๐ฎ๐ฌ๐๐ ๐๐๐ญ๐: Factories generate massive amounts of data, but much of it is never analyzed or leveraged for decision-making.
๐๐ง๐๐๐๐ข๐๐ข๐๐ง๐ญ ๐๐๐ญ๐ ๐๐๐ง๐๐ฅ๐ข๐ง๐ : Engineers waste time manually entering, cleaning, or searching for information that should be automated.
๐๐ข๐ฅ๐จ๐๐ ๐๐ง๐๐จ๐ซ๐ฆ๐๐ญ๐ข๐จ๐ง: Key insights are trapped in different departments or legacy systems, preventing AI-driven optimization.
Digital waste silently drains resources, increasing operational costs while blocking AI from delivering its full potential.
Once manufacturers recognize digital waste, the next step is identifying where AI can generate the biggest returns.
To learn more about finding opportunities for the application of AI in manufacturing, I recently sat down with Patrick Byrne, Co-Founder and CEO of Annora AI.
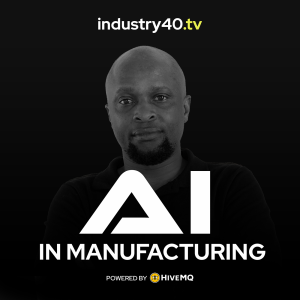
Wednesday Feb 26, 2025
Wednesday Feb 26, 2025
Manufacturers are constantly battling two critical challenges:
Inefficiencies in Equipment Usage: Downtime, slow cycle times, and unidentified bottlenecks reduce Overall Equipment Effectiveness (OEE), leading to wasted resources and missed production targets.
Safety Risks: Ensuring worker safety while maintaining productivity is difficult, especially in environments with heavy machinery and fast-moving processes.
Despite best efforts, traditional methods struggle to keep up with the complexity and speed of modern manufacturing.
By using computer vision and deep learning, Video AI Agents bring continuous, detection and response of issuesโfar beyond what traditional methods alone can achieve.
I recently sat down with Karim Saleh, Co-founder and CEO at Cerrion to learn more about how to Maximize OEE and production Line Safety with Video AI Agents
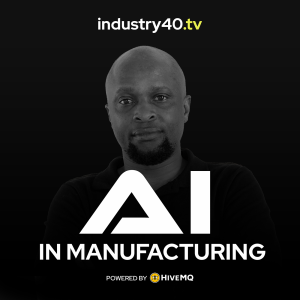
Wednesday Feb 19, 2025
Wednesday Feb 19, 2025
AIโs success in manufacturing depends on the ability to seamlessly integrate data from machines and systems across the factory floor and supply chain.
Without strong connectivity, AI remains underutilized, limited by data silos, and inconsistent integration.
Connectivity isnโt just about linking devices; itโs about creating a unified data environment where AI can operate at its full potentialโpowering everything from predictive maintenance to automated quality control and beyond.
To learn more about IT/OT connectivity for enabling AI use cases in manufacturing I had a conversation with Bernd Hafenrichter who is the CTO of soffico GmbH.
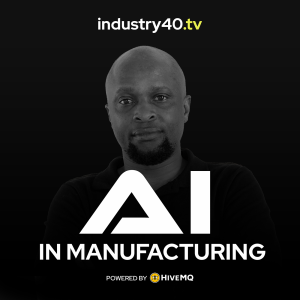
Wednesday Feb 12, 2025
Wednesday Feb 12, 2025
Frontline workers are the backbone of manufacturing, but theyโre often held back by manual data entry, process inefficiencies, and knowledge gaps.
AI-powered Industrial Copilots offer a solution that elevates their capabilities:
๐๐จ ๐๐จ๐ซ๐ ๐๐๐ง๐ฎ๐๐ฅ ๐๐๐ญ๐ ๐๐ง๐ญ๐ซ๐ฒ
AI Copilots automate data capture and seamlessly integrate with existing systemsโeliminating wasted time and inaccuracies.
๐๐ฆ๐๐ซ๐ญ๐๐ซ, ๐
๐๐ฌ๐ญ๐๐ซ ๐๐จ๐ซ๐ค๐๐ฅ๐จ๐ฐ๐ฌ
AI surfaces real-time insights, helping teams reduce downtime, optimize production, and make data-driven decisions on the fly.
๐๐ฅ๐จ๐ฌ๐ข๐ง๐ ๐ญ๐ก๐ ๐๐ฑ๐ฉ๐๐ซ๐ญ๐ข๐ฌ๐ ๐๐๐ฉ
AI-driven step-by-step guides provide instant troubleshooting and best practices, ensuring even new employees perform like seasoned experts.
๐๐๐๐ฅ๐ข๐ง๐ ๐๐ฉ๐๐ซ๐๐ญ๐ข๐จ๐ง๐ฌ
As operations grow, AI Copilots adapt to new processes, machinery, and industries, ensuring a future-proofed approach to efficiency and innovation.
To learn more about the application of AI Copilots for enhancing Frontline Operations in Manufacturing, I had a chat with Mason Glidden Chief Product and Engineering Officer at Tulip Interfaces.
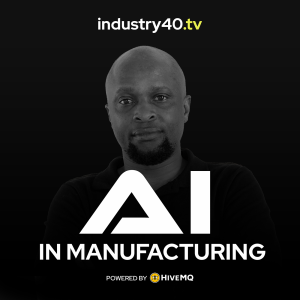
Wednesday Jan 22, 2025
Wednesday Jan 22, 2025
Many factories today grapple with recurring production issues and inefficiencies; whether itโs inconsistent quality, unpredictable downtime, or process bottlenecks.
The cost of inefficiencies keeps mounting, and while human intuition and manual checks have been valuable tools, theyโre no longer enough to drive significant breakthroughs.
AI offers an opportunity to uncover hidden patterns that human teams might miss. For instance:
- By analyzing machine sensor data, AI can trace yield drops to subtle temperature fluctuations.
- AI can identify bad material batches from suppliers or reveal operational bottlenecks.
- Instead of vague reports, AI delivers precise, actionable insights, helping teams shift from guesswork to targeted, data-driven solutions.
To learn more about how Manufacturers can achieve operational excellence through data-driven manufacturing optimisation with AI, I had a conversation with Zhitao(Steven) Gao who is the CEO and Co-Founder of eXlens.ai.
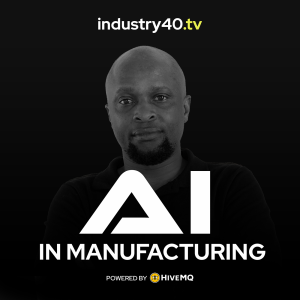
Wednesday Jan 15, 2025
Wednesday Jan 15, 2025
While the promise of AI is immense, many manufacturers find themselves stuck in pilot projects, unable to unlock its full potential.
The key lies in addressing foundational challenges and adopting a clear, phased strategy to transform operations.
Fundamentally, AI offers manufacturers a pathway to achieving operational excellence by moving through the four stages of analytics maturity:
ย
1๏ธโฃ Descriptive Analytics โ Understanding what happened.
2๏ธโฃ Diagnostic Analytics โ Pinpointing root causes.
3๏ธโฃ Predictive Analytics โ Forecasting potential equipment failures or quality issues.
4๏ธโฃ Prescriptive Analytics โ Recommending the best actions to address challenges.
Despite its promise, many manufacturers struggle with significant obstacles, which include data fragmentation.
I recently had a sit down with Andrew Scheuermann the CEO and Co-Founder of Arch Systems to discuss why building a comprehensive Digital Twin is the key to overcoming these barriers and how manufacturers can use AI to enhance manufacturing workflow efficiency.
ย
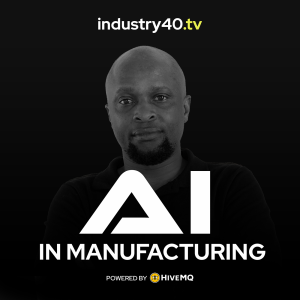
Wednesday Dec 11, 2024
Wednesday Dec 11, 2024
In our latest episode of the AI in Manufacturing Podcast, I sat down with Zeeshan Zia, co-founder and CEO of Retrocausal, to dive deep into how AI co-pilots are transforming the manufacturing sector. Here are three key takeaways:
1๏ธโฃ Labor Challenges Meet Smart Solutions
- Manufacturers face critical labor shortages, resulting in significant costs. Zeeshan shared how AI-powered Assembly Co-Pilots are slashing error rates and scrap costs by up to 90% while empowering workers with real-time guidance.
2๏ธโฃ Merging Lean Principles with AI
- Traditional lean manufacturing focuses on quality, productivity, and safety. RetroCausalโs tools like Kaizen Co-Pilot and Ergo Co-Pilot seamlessly integrate lean methodologies with advanced AI, accelerating time studies and ergonomic assessments in hours instead of weeks.
3๏ธโฃ Scalability Across Diverse Workflows
- From discrete manufacturing to medical devices, AI co-pilots are not just for single processesโthey scale efficiently across multiple sites, even in highly regulated industries.
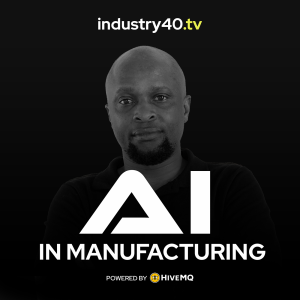
Wednesday Dec 04, 2024
Wednesday Dec 04, 2024
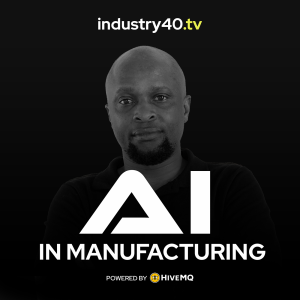
Wednesday Nov 27, 2024
Wednesday Nov 27, 2024
Today's manufacturing industry faces significant challenges in managing its data environment.
Vast amounts of unorganized data collected from various sources often become "data swamps," making it difficult to extract meaningful insights and generate value.
This overwhelming complexity hinders decision-making and slows down innovation.
Additionally, the analytics tools currently available are often too complex and static for domain experts to use effectively, leaving them without the critical insights needed to improve processes, optimize production, and make informed decisions.
AI assistants offer a promising solution by bridging the gap between complex data sets and user-friendly interfaces.
They transform unstructured data into actionable insights accessible to everyone in the organization.
To learn more about the application of AI assistants for advanced manufacturing data analytics, I sat down with Stefan Suwelack, the CEO and Co-Founder of Renumics.
ย
ย
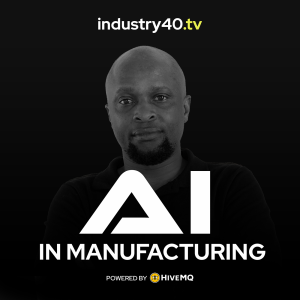
Wednesday Nov 20, 2024
Wednesday Nov 20, 2024